One of the most severe dangers that
underground petroleum of gas pipelines face, is
permanent ground deformation (PGD), such as the one
applied by the activation of seismic faults that cross
it, the lateral spreading of liquefied soils or slope
failures (cyclic or plane ground failures). The main
reason behind this is that pipelines are (a) linear
structures and as such, it is impossible for its axis to
not cross one or more fault zones or areas with possible
ground failures (landslides, lateral spreading) and (b)
because this kind of displacements are much
larger than
those applied by seismic motions and are permanent.
From
the various causes of PGD, this thesis focuses to the
design of underground pipelines versus displacements
caused by the activation of seismic faults that cross
the pipeline axis, due to fact that this kind of
displacements cannot be avoided by dealing with the
cause of the failure itself (such is the case with
ground failures where special design measures can be
taken for the local improvement of the ground in the
area, the application of drainage network, etc.), but
the pipe design must be able to resist the applied
deformations from the fault. Figure 1 presents the
deformed form of a pipeline that crosses a strike-slip
fault with a random angle.
The
common “traditional” methods for the dealing with the
applied PGD due to active fault offset can be
categorized according to the main mechanism that they
utilize in order to prevent the developed strain in the
pipeline:
(a)
reduction of the side friction between the pipe and the
ground (e.g. use of coatings – geogrids, fill with
pumice stone)
(b)
reinforcement of the pipeline ability to cope with the
applied deformations (e.g. increase of pipe wall
thickness, change of steel type), and
(c)
reduction of the ground resistance to the lateral
displacements of the pipeline near the fault area (e.g.
increase of excavation width, construction of external
underground culvert from reinforced concrete).
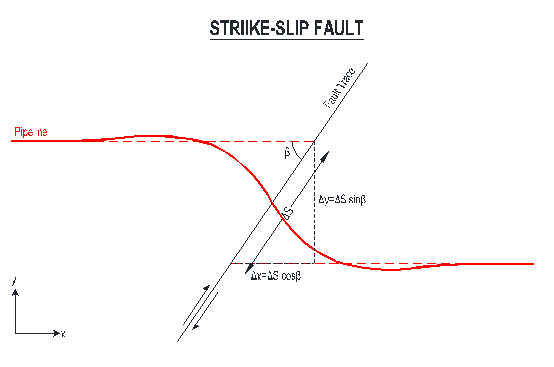
Figure
1:
Deformed
form of a pipeline that crosses a strike-slip fault
All
the above mentioned methods can be applied for small to
medium fault offsets, up to 2.5-3.0 pipe diameters.
Exception is the construction of an external culvert
from reinforced concrete, method that can protect the
pipeline against very large fault displacements, but is
expensive and its cost increases geometrically with the
increase of the fault offset. Thus, in the Geotechnical
Department of NTUA, an alternative design method with
the use of flexible joints is being researched for
pipelines at areas where large PGD are encountered. In
this research effort, a new analytical methodology has
been developed for the estimation of the beneficial
effect of flexible joints to the developing pipeline
strains.
This
thesis, as part of this research effort, focused at the
parametric investigation and evaluation of the validity
of this analytical methodology for pipelines with
flexible joints that cross strike-slip faults. In
addition, an economic-technical evaluation of the
proposed design method has been made, against the
“traditional” design methods, in order to define
practically its application limits.
From
the extensive comparison with the numerical analyses
that have been made, it is clear that the proposed
analytical methodology can accurately estimate the
phenomenon and can give accurate results for almost all
checked cases. Moreover, from the comparison of the
results between the analytical and the numerical
methodologies and the relative error of each design
parameter, the following application limits for the
analytical methodology have been defined:
·
Vertical fault offset larger than one and
a half pipe diameter (Df>1.5D)
·
Crossing angle of the pipeline with the
fault trace equal or more than 60o.
It
must be clarified that the afore mentioned limits are
not a practical limitation of the use of the analytical
methodology, since the use of flexible joints is
proposed only for large ground deformations (>2.5-3.0D).
In addition, the use of flexible joints is not
recommended when the pipeline crosses the fault with
small angle, since in this case the developing strains
are mainly due to axial deformations, and thus the use
of such flexible joints is pointless.
From
the economic-technical comparison between the proposed
design method with flexible joints and the “traditional”
methods, it has been found that their use is beneficial
for the pipe and can reduce the developing strains under
the limit strain rate of 0.5%, for fault offsets up to
3.3D when the crossing angle is 60o and up to
10D for vertical crossing angle. Thus, the proposed
design method has the largest beneficial effect between
all the “traditional” methods, except from the
construction of an external culvert.
The use of flexible joints either every 6m or 8m,
may be a more expensive method for large PGDs from the
use of pumice stone or the increase of pipe wall
thickness, but those methods have an application limit
up to 3.5D. Moreover, the use of flexible joints is less
expensive from the construction of external culvert in
most cases, and easier to be applied, since it does not
need additional construction provisions (the flexible
joints are just being welded at the selected positions).
More specifically, for vertical crossing
angle, the increase of the pipe wall thickness is
recommended for applied displacements df
≤ 3.5D, where D is the pipe diameter. The use of
flexible joints is the most effective and economic
solution for larger applied displacements 3.5D < df
≤ 10D, while, for even larger displacements df
> 10D the use of external culvert from reinforced
concrete is recommended.
For the case of smaller crossing angles, the increase of
the pipe wall thickness is recommended for applied
displacements df
≤ 3.0D, while for
larger displacements the use of pumice stone as
fill material has been found to be the best solution,
both technically and economically.